However, as standards are based on laboratory test results on cut specimens under controlled environments which do not resemble actual working conditions, the test results shall not be leveraged as indications of suitability to specific applications. To determine the gloves’ suitability, we strongly recommend trials of actual samples under desired applications. Our teams of highly experienced industrial specialists are well equipped to provide further consultations.
EN 420:2003, General Requirements for Protective Gloves
The standard provides universal requirements for the design, construction, innocuousness, comfort, efficiency, marking and all information applicable to all protective gloves. All protective gloves are given ratings based on their performance level, according to a specific test method.
REQUIREMENTS
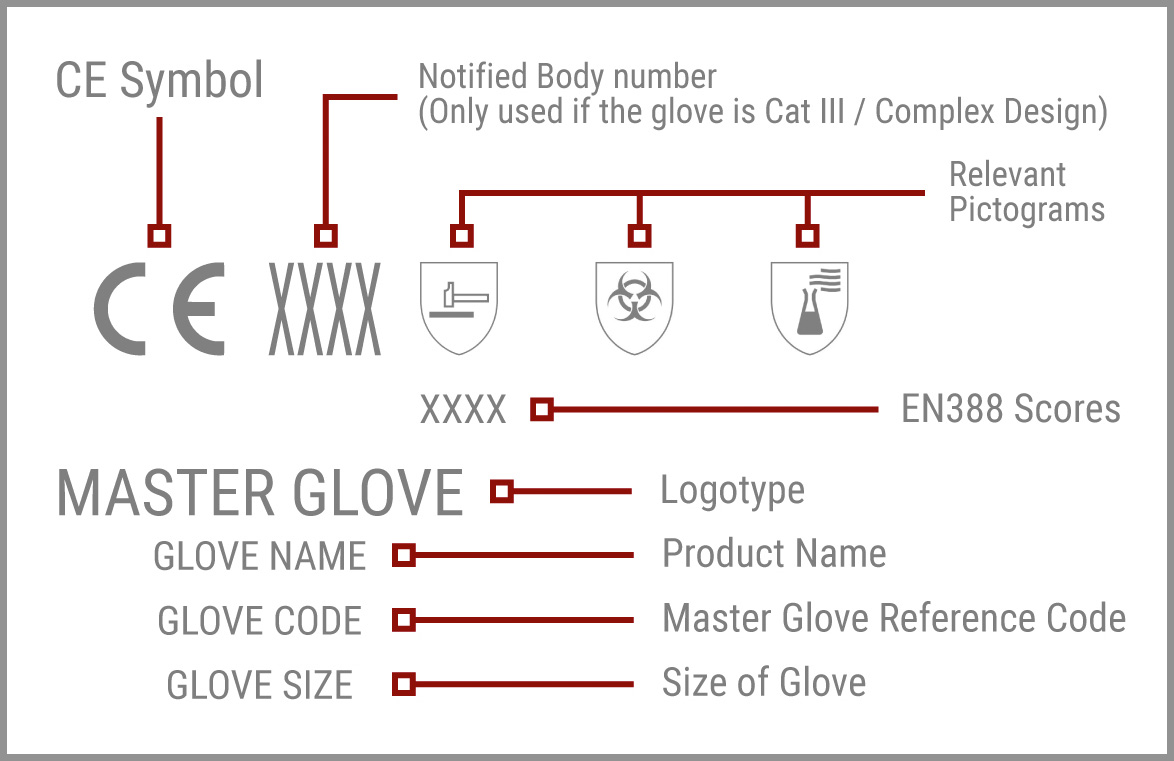
Marking and basic information
Each glove should be marked with;
-
Manufacturer’s entity
-
Glove and size designation
-
Product names
-
Product code
-
CE mark
-
Relevant pictograms
Sizing
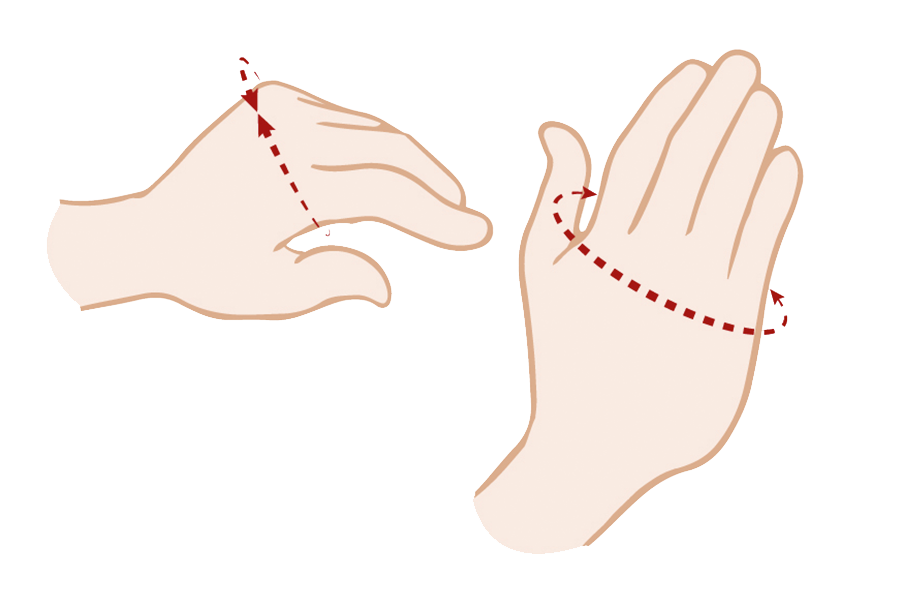
Refer to the sizing table below for appropriate sizing guidance for the gloves. Gloves that are smaller than the minimum length are to be called ‘fit for special purpose’. Glove sizes are determined according to measured hand circumferences (mm.) which is typically the dominant hand’s.
Glove Size |
Fits Hand Size |
Hand Circumference / Length (mm.) |
Minimum length of the glove (mm.) |
6 |
6 |
152/160 |
220 |
7 |
7 |
178/171 |
230 |
8 |
8 |
203/182 |
240 |
9 |
9 |
229/192 |
250 |
10 |
10 |
254/204 |
260 |
11 |
11 |
279/215 |
270 |
Dexterity
When required, glove performances are to be graded as per table below
Performance Level |
Smallest Diameter |
1 |
11.0 |
2 |
9.5 |
3 |
8.0 |
4 |
6.5 |
5 |
5.0 |
Glove construction and design
-
Gloves have to offer the greatest possible degree of protection in the foreseeable conditions of end use
Innocuousness
-
The gloves themselves should not cause any harm to the user.
-
pH of the glove should be between 3.5 and 9.5.
-
Chromium (VI) content in gloves shall not exceed 3.0 mg/kg.
-
Natural rubber glove shall be tested for extractable protein according to EN 455-3
EN 374:2003, Gloves Giving Protection from Chemicals and Micro-Organisms
This Standard specifies the capability of gloves to protect the user against chemicals and/or micro-organisms.
DEFINITIONS
Penetration
The movement of a chemical and/or micro-organism through porous materials, seams, pinholes or other imperfections in a protective glove material at a non-molecular level.
Permeation
Permeation is a process by which molecules diffuse through a membrane by means of diffusion process. Molecules move from region with higher concentration to that with lower ones. As liquids are capable of diffusing through rubber films, it is vital to determine the breakthrough times which is the time taken from the liquid to come into contact with the skin through the glove’s rubber film.
REQUIREMENTS
Penetration
A glove shall not leak under an air and/or water leak test and shall be tested and inspected in compliance with the Acceptable Quality Level (AQL).
Performance Level |
Acceptable Quality Level Unit |
Inspection Levels |
Level 3 |
< 0.65 |
G1 |
Level 2 |
< 1.5 |
G1 |
Level 1 |
< 4.0 |
S4 |
Permeation
Each chemical test is classified in terms of breakthrough time with varied performance level
MeasuredBreakthough Time |
ProtectionIndex |
MeasuredBreakthough Time |
ProtectionIndex |
> 10 minutes |
class 1 |
> 120 minutes |
class 4 |
> 30 minutes |
class 2 |
> 240 minutes |
class 5 |
> 60 minutes |
class 3 |
> 480 minutes |
class 6 |
PICTOGRAMS
Chemical Resistant
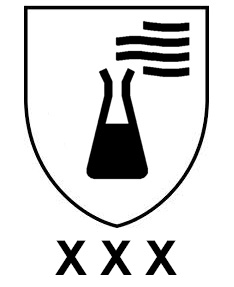
The ‘chemical resistant’ pictogram must be accompanied by a minimum of 3-letter code. This code refers to the code letters of three chemicals (from a list of 12 defined chemicals) for which a breakthrough time of at least 30 minutes has been recorded.
Code Letter |
Chemical |
Cas Number |
Class |
A |
Methanol |
67-56-1 |
Primary Alcohol |
B |
Acetone |
67-64-1 |
Ketone |
C |
Acetonitrile |
75-05-8 |
Nitrile Compound |
D |
Dichloromethane |
75-09-2 |
Chlorinated Paraffin |
E |
Carbone Disulphide |
75-15-0 |
Sulphur Containing Organic Compound |
F |
Toluene |
108-88-3 |
Aromatic Hydrocarbon |
G |
Diethylamine |
109-89-7 |
Amine |
H |
Tetrahydrofurane |
109-99-9 |
Heterocyclic and Ether Compound |
I |
Ethyl Acetate |
141-78-6 |
Ester |
J |
n-Heptane |
142-85-5 |
Saturated Hydrocarbon |
K |
Sodium Hydroxide 40% |
1310-73-2 |
Inorganic Base |
L |
Sulphuric Acid 96% |
7664-93-9 |
Inorganic Mineral Acid |
Micro-Organism
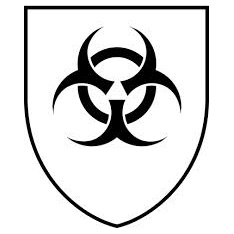
The ‘Micro-Organism’ pictogram above is to be used when the glove conforms to a minimum of level 2 for the penetration test.
Low Chemical Resistant
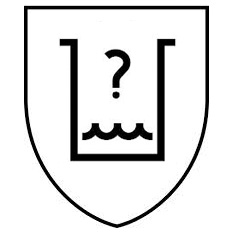
The ‘Low Chemical Resistant’ or ‘Waterproof glove’ pictogram is to be used for gloves which fail to achieve a breakthrough time of at least 30 minutes against a minimum of three chemicals from the defined list, but able to comply with the penetration test.
EN 388:2003, Glove Giving Protection from Mechanical Risks
This Standard is applicable to all kinds of protective gloves in relation to physical and mechanical pressure enforced upon by abrasion, blade cut, tear and puncture.
The pictogram expressing mechanical risks is expressed alongside a 4-digit code. A total of four mechanical hazard tests are to be taken, as classified below;
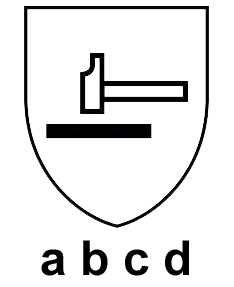
a) Resistance to Abrasion
Determination of the number of cycles required to abrade through the sample glove
b) Blade Cut Resistance
The number of cycles required to cut through the sample at a constant speed
c) Tear Resistance
Amount of force required to tear the sample
d) Puncture Resistance
Force required for a standard-sized point to pierce through a sample
There are five performance ratings to each test, with 0 indicating lowest performance level and 5 indicating otherwise
Test |
Performance Level Rating |
|||||
0 |
1 |
2 |
3 |
4 |
5 |
|
a) Resistance to Abrasion |
< 100 |
100 |
500 |
2,000 |
8,000 |
|
b) Blade Cut Resistance |
< 1.2 |
1.2 |
2.5 |
5.0 |
10.0 |
20.0 |
c) Tear Resistance |
< 10 |
10 |
25 |
50 |
75 |
|
d) Puncture Resistance |
< 20 |
20 |
60 |
100 |
150 |
Performance level must be vividly displayed beside the pictogram on the gloves and also on the packaging containing the gloves.
EN 407:2004, Gloves Giving Protection from Thermal Hazards
This Standard indicates thermal performance for protective gloves against heat and/or fire. The nature and degree of protection is illustrated by a pictogram accompanied by six performance levels, relating to specific protective qualities.
A six-digit number accompany the ‘heat and flame’ pictogram to indicates the glove’s performance level in each respective category.
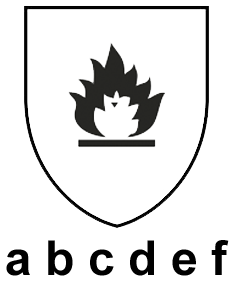
a) Resistance to flammability (performance level 0-4)
The length of time the material continues to burn and glow after the source of ignition is removed. The seams of the glove shall not come apart after an ignition time of 15 seconds.
b) Contact heat resistance (performance level 0-4)
The test is based on the temperature range of 100°C-500°C (212°F-932°F) at which the user will feet no pain for at least 15 seconds. If an EN Level 3 or higher is obtained, the product shall obtain at the minimum of EN Level 3 in the flammability test. Otherwise, the maximum contact heat level shall be reported as Level 2.
c) Resistance to convective heat (performance level 0-4)
Determined by the length of time the glove is able to delay heat transfer from a flame. A level of performance shall only be mentioned if a Performance Level 3 or 4 is obtained in the flammability test.
d) Resistance to radiant heat (performance level 0-4)
Determined by the length of time the glove is able to delay the transfer of heat when exposed to a radiant heat source. A level of performance shall only be mentioned if a Performance Level 3 or 4 is obtained in the flammability test.
e) Resistance to small splashes of molten metal (performance level 0-4)
The number of molten metal drops required to heat the glove sample to a given level. A level of performance shall only be mentioned if a Performance Level 3 or 4 is obtained in the flammability test.
f) Resistance to large splashes of molten metal (performance level 0-4)
The weight of molten metal required to cause smoothing or pin holing across a simulated skin placed directly behind the glove sample. The test fails if metal droplets stick to the glove material or if the specimen ignites.
Gloves must achieve at least performance level 1 for abrasion and tear
EN 511:2006, Gloves Giving Protection from cold
This Standard is applicable to any gloves designed to protect the hands against convective and contact cold at low temperature of up to to -50°C (-58°F).
Protection against cold is expressed by a pictogram followed by a range of three performance levels, relating to specific protective qualities. The pictogram is accompanied by a three-digit number
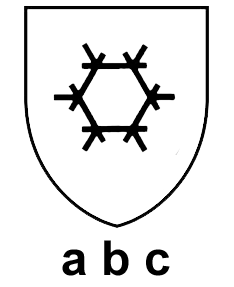
a) Resistance to convective cold: (performance level 0-4)
Determine the thermal insulation properties of the glove obtained by measuring the transfer of cold via convection.
b) Resistance to contact cold: (performance level 0-4)
Based on thermal resistance of the glove material when contacted with a cold object
c) Penetration by water (0 or 1)
0 = water penetration , 1 = no water penetration
All gloves must achieve at least performance level 1 for abrasion and tear
EN 421:2010, Gloves Giving Protection from radioactive contamination and ionizing radiation
This Standard applies to gloves offering protection from ionising Radiation and Radioactive Contamination
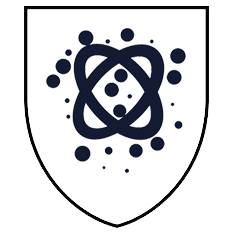
The nature of protection is shown by a pictogram relating to specific protective qualities
To protect from radioactive contamination, the glove has to be liquid proof and is required to pass the penetration test as defined in EN 374.
For gloves used in containment enclosures, the glove should be able to pass specific air pressure leak test.
Material may be modeled by their behavior to ozone cracking. This test is optional and can be used as an aid to selecting gloves
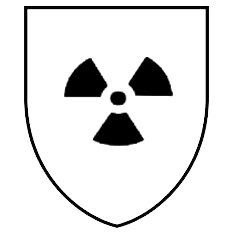